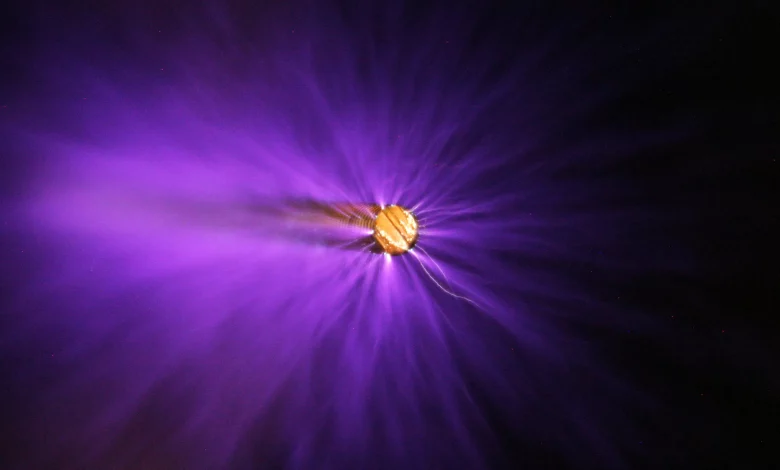
What does the future of automobiles look like? The answer, it turns out, varies wildly from expert to expert. Some say that the cars of tomorrow will be fitted with hydrogen engines. Others say that the coming years will be characterized by the slow and steady transition from the internal combustion engine to the more traditional electrical vehicles being developed by Tesla and others.
But whatever path we take as we transition from internal combustion engines, it needs to be a long one. If we try and transition too quickly, it could prove to be incredibly destructive (to put it very mildly).
Fortunately, as it turns out, there is an emerging technology that could fill the gap until we have a mass rollout of electric vehicles and the charging infrastructure needed to power them all.
The technology is called “transient plasma ignition,” and it could, in theory, boost the efficiency of internal combustion engines by as much as 20 percent and reduce NOx by more than 50 percent. Not too shabby.
In fact, this technology could prove to be revolutionary and, in some ways, save the internal combustion engine. We’ve recruited Dan Singleton, founder, and CEO of Transient Plasma Systems (TPS), to help explain.
What is plasma?
Plasma ignition technology, like that developed by TPS, makes use of low-temperature plasma generated by nanosecond electrical pulses, also called transient plasma, to greatly boost the combustion process. The plasma primarily acts as a kind of catalyst for ignition.
Plasma, either natural (like in the sun) or atmospheric plasma (when gas is excited by means of a high voltage at atmospheric pressure in such a way that a plasma is generated) is one of the four fundamental states of matter that has some very unique properties that make it very useful for certain applications – like ignition.
An ionized gas, plasma is a mixture of charged particles that behaves far differently than standard gas. The naturally-occurring plasma that makes up a star is extremely hot and in thermal equilibrium. In other words, the electrons and ions are at approximately the same temperature.
Artificial plasmas, on the other hand, come in a variety of “flavors” depending on how they are generated. One kind is called artificial thermal plasma, like those created by welding arcs.
Another is artificial non-thermal plasma, which is the type of plasma often found in industrial environments. It is this second kind that is used in applications like transient plasma ignition systems.
In these kinds of plasmas, the electrons and ions are not in thermal equilibrium. This is by design so that the energetic or “hot” electrons can accomplish something useful, such as breaking a chemical bond, while the energy imparted to the “cool” ions and neutral species is minimized.
Because the ions and neutrons account for nearly all of the mass of the plasma stream, keeping them cool avoids the extreme heat associated with thermal plasmas.
In atmospheric-pressure industrial plasma, energy is provided to the plasma by applying an electrical voltage that accelerates charged particles. The electrons are much lighter (have much less mass) than the ions, so they respond much more rapidly and zip around at speeds roughly 100x faster than the ions.
These electrons quickly gain enough energy to ionize additional particles, creating more free electrons to break bonds or provide the activation energy needed for desired chemical reactions. This is incredibly efficient because the reaction rates driven by energetic electrons can be up to 1,000x faster than the ones driven by thermally heating the reactants.
Thus, artificial non-thermal atmospheric plasmas can be used to drive efficient, fast chemical reactions – like in internal combustion engines. Such plasmas have other useful functions too like ozone generation, cleaning, decontamination, surface activation to improve bonding, curing of coatings, and functional thin-film deposition.
But, more on that later.
What is transient plasma ignition?
Plasma ignition systems, like those in development by Transient Plasma Systems, work by releasing a nanosecond electrical pulse to create a high power, low-energy plasma pulse. The pulse is not hot but has enough energy to immediately ignite the gasoline-air mix in an internal combustion engine.
A transient plasma system, as opposed to other types of plasma ignition systems, is fundamentally different, because each high-voltage pulse is applied for only 10-20 nanoseconds.
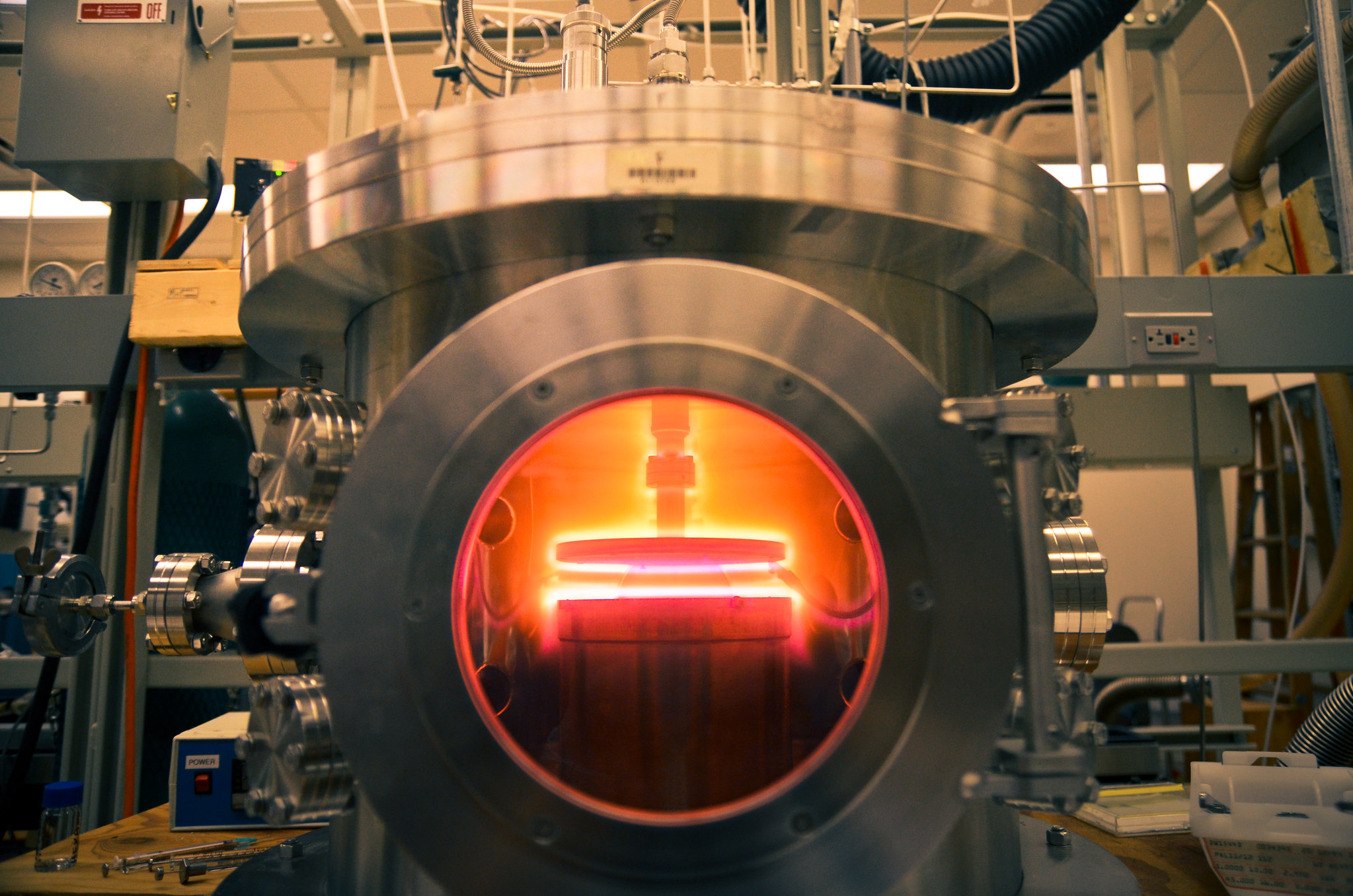
During each incredibly fast, high-voltage pulse, the extremely light electrons rapidly gain the energy needed for industrial applications. As previously explained, this setup means the more massive ions don’t have time to absorb energy, and they are effectively stationary during the pulse.
This type of nanosecond-pulse plasma is used to help drive many chemical reactions in various industrial and manufacturing applications too like cleaning surfaces before they are painted, activating rubber for better adhesion, or applying thin-film coatings on glass. Or, in this case, improving the combustion process in a gasoline engine.
The released plasma, namely the free-electrons within it, collide with the air-fuel mixture in the piston. This produces chemically reactive species that catalyze the combustion process and, in turn, enhance ignition and stabilize lean-burn combustion.
The spatial distribution of plasma in systems like the Transient Plasma Ignition System enables a single streamer discharge to impact a large volume.
“The TPS Transient Plasma Ignition System uses a nanosecond electrical pulse to generate plasma, to create instantaneous high power at a much faster rate than a traditional spark. This high-power but low energy pulse creates low-temperature plasma that will not light a match, yet ignites dilute air-fuel mixtures efficiently and immediately,” explained Dan Singleton to Interesting Engineering.
In this process, more fuel is actually turned into useful energy reducing the amount of fuel needed for the same output, and, by extension, greatly boosting fuel efficiency.
As Singleton explained, transient plasma offers, “faster combustion, stable ignition at higher compression ratios, and improved combustion timing. The result is an ignition solution that allows engines to use highly dilute burn modes (dilute with EGR or lean with air), which increase fuel efficiency and reduce greenhouse gas emissions. Conventional ignition systems struggle to ignite dilute air-fuel mixtures”.
Such systems can be installed in existing engines with a little modification. For example, the system developed by TPS consists of an electronics module that is powered directly from the vehicle’s main battery.
“Our nanosecond pulsed-plasma ignition system works in tandem with the engine designs and other efficiency improvement technologies deployed by original equipment manufacturers (OEMs), adding to the eco-friendly benefits of these solutions,” added Singleton.
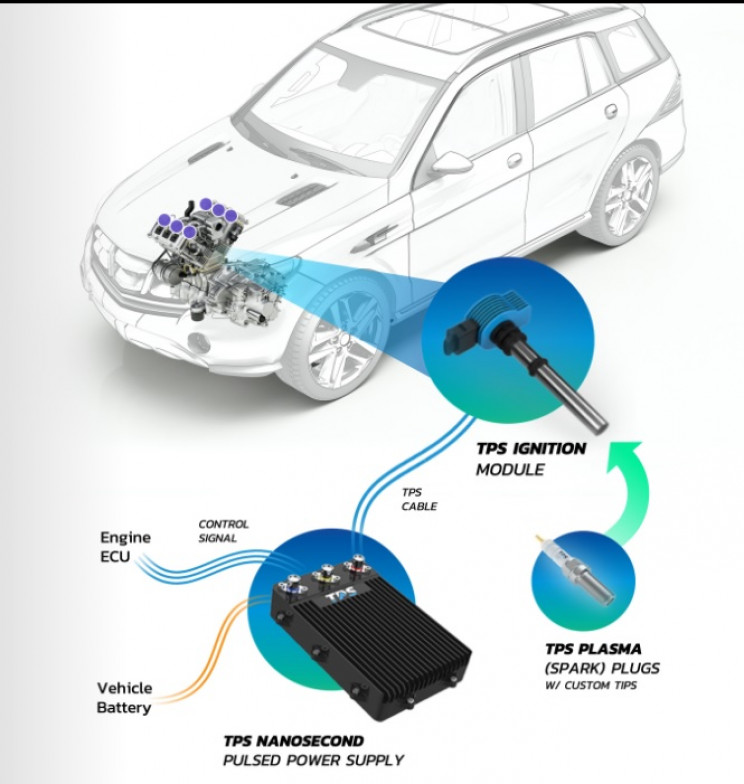
he module, or pulsed power supply, communicates with the engine control unit (ECU) providing ignition pulses as needed. This plasma power supply is, in turn, connected to a set of standard spark plugs that have modified electrodes to provide optimal performance.
The technology can be applied to most, “gasoline and natural-gas fuelled engines found in passenger vehicles, commercial vehicles, and off-highway applications such as construction equipment or power generators,” Singleton told us.
But it gets better.
“Furthermore, the TPS Transient Plasma Ignition System amplifies other efficiency improvements developed by automotive OEMs. Unlike competing systems that involve costly engine redesigns and displacement of current combustion-engine architecture, the TPS ignition system works in tandem with existing engine designs and efficiency techniques such as exhaust gas recirculation (EGR), gasoline direct injection (GDI), turbocharging, and e-boost, significantly enhancing fuel economy and emissions reduction through a simple plug-and-play solution (i.e., no modifications to the OEM engine are needed),” Singleton added.
All very exciting, but we’ll have to wait a little longer before you can get your hands on one.
“TPS technology is being evaluated by several players in the transportation industry. The earliest potential launch date is mid-2023,” hopes Singleton.
Are there any limitations to plasma ignition?
Like so many things in life, there is not a perfect solution to any problem, only compromises. The same is definitely true for plasma ignition.
Most modern industrial plasma systems are driven by oscillating high voltages ranging from a few hertz to gigahertz. When energy is applied on a time scale lasting longer than 100 nanoseconds, the heavier ions have sufficient time to absorb some of the energy and play a more active role in the discharge.
When ions and neutral species are heated up, thermal instabilities can build up in the plasma – which is a potential problem. You can see this demonstrated when plasma changes from a uniform glow to a more chaotic collection of lightning bolts in a plasma globe.
This can lead to arcs or sparks forming that can make the plasma non-uniform and potentially damaging to the target substance of the process. This would be counterproductive, to say the least.
To avoid this, most industrial plasmas tend to be driven by long pulses of steady or oscillating voltages that must be kept within a very tight and controlled window. This is a fine balance, as it must be able to provide the plasma with enough energy to drive the desired reaction, but not too much to create a potentially very unstable plasma, as described above.

When operating at atmospheric pressure, this delicate balance must be carefully controlled to avoid the transition to a higher temperature, unstable thermal plasma. This is not easy.
This is where transient plasma comes into its own. It, in effect, manages to strike a balance by reducing the risk of thermal instability, thereby resulting in a much more easily manageable and tunable plasma.
Transient plasma is characterized by electrons that rapidly gain energy from extremely short and precisely controlled-high voltage pulses. As such, transient plasma electrons perform the same useful functions as those in an industrial atmospheric-pressure plasma system, but with additional advantages in terms of efficiency and versatility.
This use of extremely short, yet intense, pulses within transient plasma enables ions and neutral species to remain consistently cool. This is mainly because they do not have enough time to absorb enough energy to become unstable.
By virtue of this, transient plasma systems eliminate the risks of arcing and thermal instability, enabling versatile operation over a wide range of pulse amplitudes, pulse repetition rates, and gas-flow rates. This is incredibly useful and enables transient plasma systems can be used to enable a wider variety of applications as compared to conventional industrial atmospheric-pressure plasma systems.
Pretty awesome.
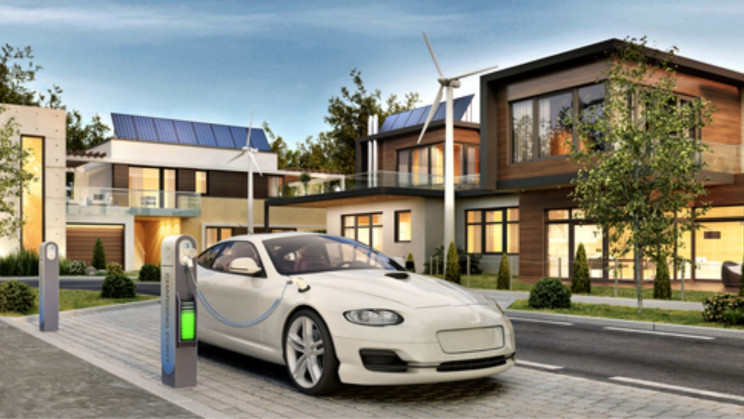
It could also be the key to allowing us to fully transition to EVs.
“We know electric vehicles are coming, but they won’t arrive overnight, and internal combustion engines (ICEs) won’t disappear overnight,” Singleton told IE.
“However, that doesn’t mean we can’t address the climate crisis right now by continuing to improve ICEs and reducing emissions. We believe Transient Plasma Ignition technology is the last significant improvement that can be made to ICEs, which can be implemented as a plug-and-play solution to existing ICE designs at a minimal cost to OEMs,” he added.
“Additionally, until EVs become ubiquitous, ICE vehicles will continue to be produced, sold, used, and will pollute for decades. It’s imperative that we make these vehicles cleaner and TPS technology can definitely help with that,” Singleton explained.
All very interesting, but how does it all work?
How does plasma ignition work?
Since this system is primarily designed for combustion engines, it might be worth spending some time briefly covering how ignition is created in existing combustion engines.
At their very core, internal combustion engines rely on the chemical process of combustion of a fuel and air mixture to release energy. This energy is then put to work to provide mechanical work of some kind, like turning a shaft.
To this end, a typical engine consists of a fixed cylinder and a moving piston. The expanding combustion gases push the piston, which in turn rotates the crankshaft. Ultimately, through a system of gears in the powertrain, this motion drives the vehicle’s wheels.
At present, the two most common forms of the engine in use are spark-ignition gasoline engines and compression ignition diesel engines, though the latter is obviously being phased out in many countries around the world. In most cases, these engines are what is termed four-stroke, which means that four piston strokes are needed to complete one cycle.
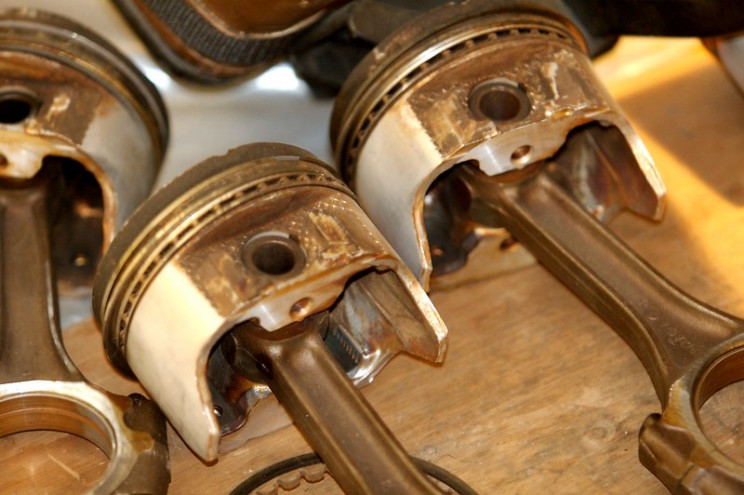
A “cycle” includes four main processes: intake, compression, combustion and power stroke, and exhaust.
The main difference between the two types of engines is in the way that fuel (and air) is suppled and ignited in the engine. In spark-ignition gasoline engines, fuel is mixed with air and then introduced into the cylinder during the “intake” phase of an engine cycle.
This mixture is then compressed and ignited by an electrical spark from the spark plug. The expansion of the combustion gases pushes the piston during the power stroke, and the rest is history.
For diesel engines, only air is inducted into the engine and is compressed to a further extent. Diesel engines then spray a mist of fuel into the hot compressed air at a suitable, measured rate, causing it to ignite.
For gasoline engines, this process leads to the degradation of the spark plugs over time due to a build-up of carbon on exposed electrodes after many cycles of the engine. Eventually, the build can get so bad, that the plugs will need to be replaced or refurbished, every 30,000 miles, or so.
Unlike traditional spark plugs installed in most internal combustion engines, plasma ignition systems are considerably more efficient over time.
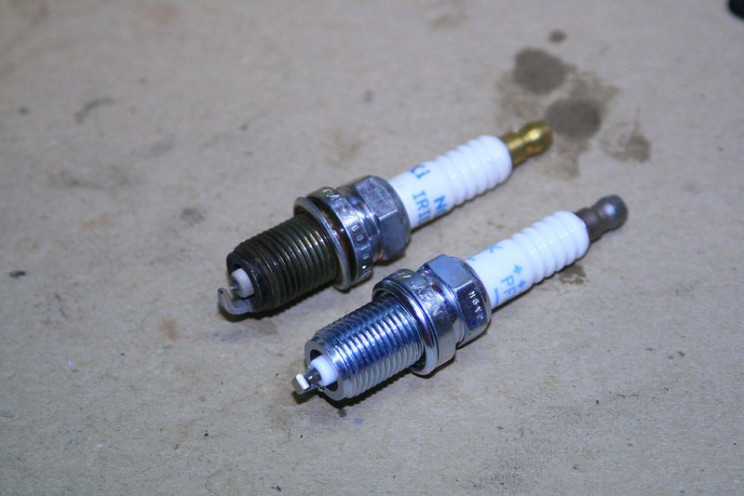
By replacing the plugs with plasma ignition devices, carbon build-up in this fashion is greatly reduced. Not only that, but emissions, especially potentially harmful NOx emissions, can be cut by as much as 50%.
Transient plasma ignition also has other very important advantages over more traditional ignition systems.
For example, TPS ignition enables, attributes that improve engine efficiency, such as
- Higher compression ratio
- Increased specific heat ratio
- Faster combustion
- Improved combustion timing
- Increased knocking resistance
- Reduced heat-transfer losses
- Reduced pumping losses
Transient plasma has many other applications beyond boosting ICE efficiency
As exciting as transient plasma seems to be for the near-to-medium term of internal combustion engines, it could have some other very important applications too. Here are some of the most notable examples.
1. Transient plasma is handy for cleaning and decontamination
One key is that transient plasma could be very useful is for cleaning and decontamination. This kind of plasma is extremely effective at removing materials like carbon and carbonate contamination from aluminum surfaces, for example.
This is useful in and of itself, but transient plasma also leaves behind no material residues to boot. This is incredibly useful for cleaning things like electrodes, increasing their potential working life, and reducing erosion. Transient plasma can also be used to improve surface adhesion for the application of paints, adhesives, and other types of coatings.
2. Thin-film coating could benefit greatly from transient plasma
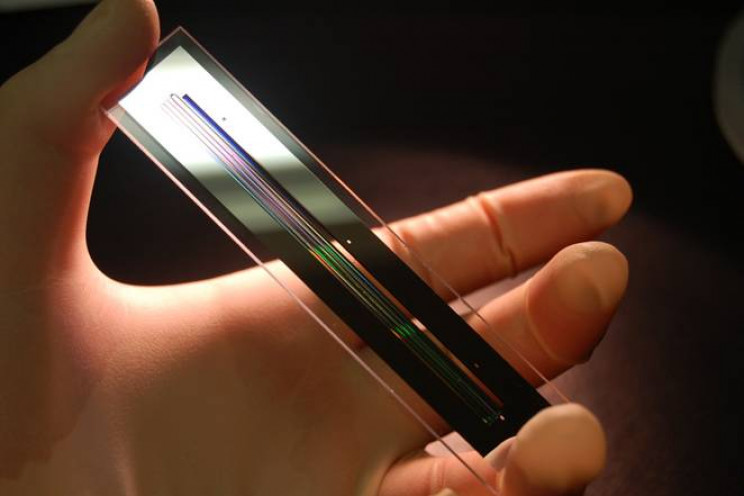
The unique properties of transient plasma make an ideal solution for processes that rely on uniform and high-integrity thin-film coatings. This is vital for various industries including biomedicine, aerospace, etc.
Transient plasma can be used to deposit amino groups that will not degrade during the application process and are also stable against even the most aggressive of washing processes. The precise tunability of transient plasma systems also enables defect-free “single sweep” coatings.
As Singleton told IE, “TPS technology can also be used for surface treatment of different substrates, creating novel and hard to achieve properties. TPS has collaborated with a prominent German national lab that has expertise in surface treatment, and that work has demonstrated promising results.”
3. Transient plasma is very useful for activation
Another important application of transient plasma is activation. Transient plasma can be applied to a range of substrate materials including, but not limited to, metals, polymers, and other temperature-sensitive materials.
For any laboratory work that uses polypropylene, Ethylene Propylene Diene terpolymer (EPDM), and silicone substrates, transient plasma has proved to be very versatile in the areas of cleaning, chemical modification (activation), preparing substrates for subsequent processing, and adhesive bonding.
4. Transient plasma can be used to replace harmful chemicals too
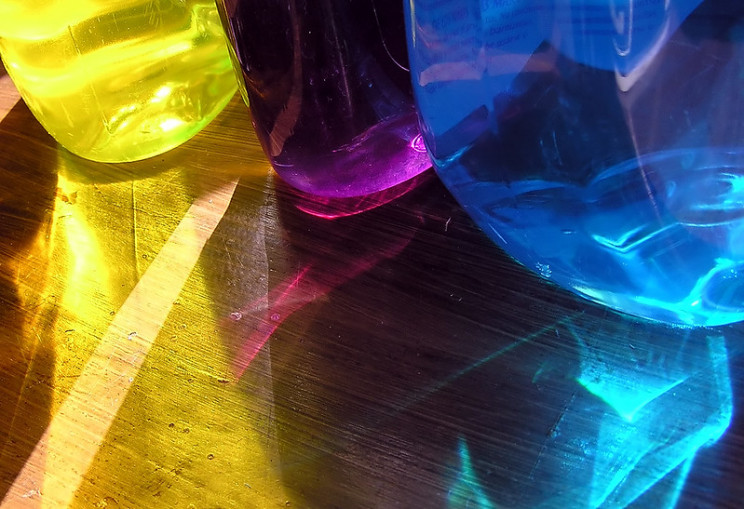
Many industries use chemicals or atmospheric-pressure plasma systems to treat surfaces and apply uniform surfaces like thin-film coatings, as previously mentioned. However, for the former, this usually involves submerging materials in chemical baths that often contain hundreds of gallons of toxic chemicals.
These chemicals are not only potentially harmful to use and handle, but they also need to be disposed of after use. If not disposed of properly, they can damage the environment and the disposal can be difficult and expensive, forcing organizations to spend a lot of money on meeting the myriad regulations in place in many countries around the world.
But even with the best planned and managed toxic waste systems, there is still the risk of these chemicals accidentally entering the biosphere. Again, this leads to the need for organizations to spend large amounts of money managing their waste streams.
But this is only part of the problem. Chemically treated materials usually also need to be dried or cured using heat. This can consume a lot of energy to achieve, not to mention the potential for other ancillary harmful emissions when generating the power needed.
In addition to atmospheric-pressure plasma systems, some manufacturing environments use chemical processes to treat surfaces and apply uniform thin-film coatings. These processes require chemical baths, and hundreds of gallons of potentially toxic chemicals must be disposed of after usage – a waste stream that often ends up harming the environment.
A transient plasma system, on the other hand, is capable of applying thin-film coatings and treating surfaces just as effectively as these chemical processes but for a fraction of the energy costs. Transient plasma also does not need a large number of chemicals to achieve the same outcome, and effectively eliminates expensive waste logistics or post-treatment drying.
It is, therefore, a much cleaner, greener, and cost-effective solution for the same applications.
5. Transient plasma is more versatile than other plasma treatments, like vacuum plasma
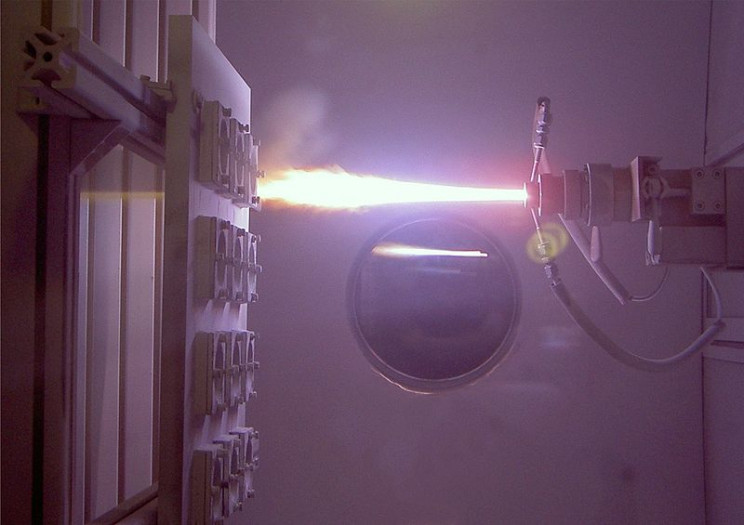
As previously mentioned, most existing industrial plasma systems must work within a very fine-tuned range of conditions. When operating at atmospheric pressure, this delicate balance must be carefully controlled to avoid the transition to a higher temperature, unstable thermal plasma.
This usually requires the plasma treatment to be performed in a vacuum.
Not only that, but many manufacturing lines using low-pressure plasma systems utilize batch processing to reduce overall throughput, compared to an all atmospheric pressure line.
With a transient plasma system, however, end-users can perform many of the applications normally done in a vacuum plasma chamber in an open-air setting. This is a much more convenient and cost-efficient alternative to vacuum plasma treatment.
6. Transient plasma could help clean up diesel engines
While transient plasma ignition technology, like that in development by TPS, is mainly aimed at gasoline engines, it can, with some modification, be used to improve diesel engines, too.
As Singleton explained to IE, “with respect to diesel engines, TPS technology can be applied at the exhaust end to reduce emissions (particulates, NOx, etc.). The results from some initial testing by TPS under a DOE grant have been encouraging. This diesel emissions remediation solution is still under development since the focus of TPS has been on ignition.”
Perhaps, just perhaps, diesel engines could see something of a comeback thanks to transient plasma in the future? Or at least the remaining diesel engines could be made somewhat less polluting.
What is the future of transient plasma?
Dan Singleton is very confident about the future of transient plasma technology. This is mainly because he believes, like many, that the internal combustion engine will not completely disappear.
“We believe that some combustion engine applications will continue to be necessary for a long time to come, such as medium-heavy duty trucks, emergency power generation, etc,” Singleton told IE.
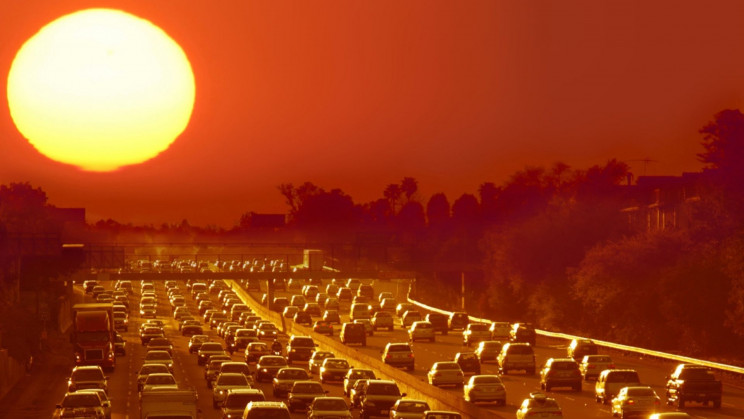
But, as we’ve seen above, transient plasma technology has applications outside of improving ICEs.
“TPS technology has multiple applications in addition to ignition and emissions reduction from combustion engines. TPS technology can reduce emissions from commercial kitchens, a significant issue in urban areas, and one that regulatory authorities want to limit via more stringent regulations but haven’t done so because of the lack of availability of cost-effective solutions,” Singleton told us.
“TPS has demonstrated the efficacy of its solution via work done with a major kitchen ventilation equipment provider,” he added.
And that “plasmaphiles” is your lot for today.
Transient plasma technology is not only incredibly interesting as a concept, but happens to have some very important benefits to many industrial, commercially, and even domestic processes – including reducing running costs for your car.
It also potentially unlocks several novel capabilities of plasma in atmospheric applications, leading to potentially exciting outcomes in several applications. Those benefits begin with greater stability, a more versatile range of operating parameters, superior tunability, and the ability to create a large volume of uniform plasma.
They continue with the ability to create low-temperature plasma that can be used to treat heat-sensitive substrates, including human tissue. But that is something for another time.
For now, perhaps, just perhaps, transient plasma could prove to be the stopgap needed before we, as a society, can complete the transition to fully electrical, hydrogen-powered, or who knows, even micro-nuclear vehicles.